When Highways England introduced its Road Investment Strategy: 2015 to 2020, it was designed to provide a network for the future, that will be smoother, smarter and more sustainable. This involves the efficient movement of people and goods, utilising technology to deliver safer roads and ease congestion and delivering economic, environmental and social benefits.
The strategy supports Highways England’s design vision “to put people at the heart of our work by designing an inclusive, resilient and sustainable road network; appreciated for its usefulness but also its elegance, reflecting in its design the beauty of the natural, built and historic environment through which it passes, and enhancing it where possible.”
The Road Investment Strategy was followed by the launch of Highways England’s first Sustainable Development Strategy last year.
Its aim is to encourage economic growth, while protecting the environment and improving safety and quality of life for current and future generations, with Highways England adhering to the principles of sustainable development in everything it does.
There are five main concepts in the Sustainable Development Strategy:
- Financial capital, or the capacity to invest
- Human capital, or the knowledge and capacity of the workforce and stakeholders
- Natural capital, or the natural resources and services
- Social capital, or the relationships, networks and communities
- Manufactured capital, or the infrastructure and technologies
For each ‘capital’, Highways England has identified a ‘vision’ and ‘ambition’ in the Sustainable Development Strategy. To turn the visions into a reality, the company is setting about delivering a series of focused actions.
The 2015-2020 roads period will be a time of significant investment in England’s roads. Through this investment, Highways England will improve the condition of its assets and increase its ability to cope with change. Assets are designed using rigorous standards to produce infrastructure that lasts, and the company is seeking to ensure resilience to climate change so it is embedded in its business activities to reduce costs and increase safety.
The sustainable strategy will ensure climate change is considered in the future standards within the Design Manual for Roads and Bridges. This begins with a general requirement that the goals of sustainable development shall be delivered throughout the design lifecycle, including that the design shall aspire to be resilient to future climate change. Existing adaptation plans are also being reviewed.
The agency aims to deliver a meaningful contribution to the UK Government target of an 80% reduction in greenhouse gas emissions, against the levels in the 1990s, by 2050. Carbon reduction is a key requirement of Highways England’s licence and the Road Investment Strategy makes commitments to adopting low carbon technology. This has seen Highways England investigating low carbon technology use on the strategic road network.
The Sustainable Development Strategy describes the unique priorities, visions and ambitions for sustainable development. This strategy is designed to communicate the company’s approach and priorities for sustainable development to its key stakeholders. This, alongside other strategies and plans, will contribute to the sustainability of the company and the strategic road network. Highways England is keen to ensure its actions in the future will further reduce the adverse impact of its activities seeking a long-term and sustainable benefit to the environment and the communities it serves.
Current objectives for the agency are to: remove energy-inefficient lights from the network; improve the operation of energy-consuming assets; and to get inventories accurate.
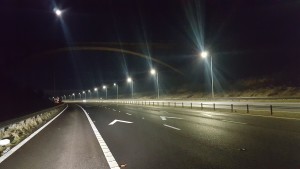
Efficient LED lighting on the M621
One project on which Highways England has implemented this policy is on the M62 and M621 near Leeds, where 1,618 street lights have been replaced with modern efficient LED lighting units.
New efficient technology for signals and road lighting can achieve a 30% energy reduction if converted to LED, plus, another potential 20% through smart management of lighting levels. On the M62 J22-J25 scheme, Highways England approached specialist lighting companies in order to adapt sodium lighting technology for the motorway. This type of solution is commonplace for architectural ornamental lighting, such as monuments and halls, but this is the first time it is being used to light a highway.
The new lighting is 53% more efficient, saving more than 700 tonnes of carbon a year, energy equivalent to powering the homes of 20,000 people and 389,000 loads of washing. Further benefits include the need for minimal maintenance, meaning less disruption for drivers.
Works also included the upgrading of power supply equipment on both roads, while a remote monitoring system was also installed to control the new lights.
Highways England’s Service Delivery Team Leader for Yorkshire and Humber, Mark Ramsden, said: “This is a true example of taking innovation from another industry, modifying it for the highways sector, and improving value by locking in safety, customer, cost efficiencies and environment benefits.
“We have replaced the conventional lighting with the newly developed lighting to provide bright, effective illumination to highways and road signs – reducing maintenance and road closures for drivers.”
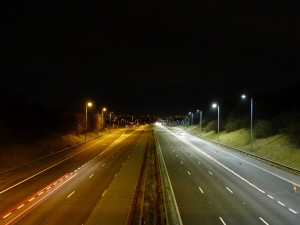
The difference between LED and traditional lighting.
Another example of the policy in action is on the A160 upgrade scheme. The upgrading of the A160 between the A180 Brocklesby Interchange junction and Immingham Harbour was seen as a priority project for Highways England to improve access to the Port of Immingham.
The scheme started in spring 2015 and was completed in spring last year. Highways England worked collaboratively with its suppliers to deliver the much-needed upgrade. More than two years before work started on site, the project partners undertook a rigorous research programme to ensure the design and delivery of the scheme had sustainability at its heart. Core samples taken from the existing road identified tar-bound asphalt, a hazardous waste material – a constraint. To divert the 2,800 tonnes of planings from landfill, a supplier suggested that they be encapsulated in the sub-base cement-bound granular mix material as part of a total of 30,000 tonnes of recycled aggregates used in the project – the opportunity.
Early engagement across the supply chain also ensured that innovations such as lower temperature asphalt were built into the road design, saving more than 200 tonnes of carbon dioxide equivalent.
If you would like to read more articles like this then please click here.
The post Paving the way for a greener future appeared first on UK Construction Online.