In this article, Geoff Fawkes, Director of The McAvoy Group, looks at how offsite construction is helping to address the housing crisis by increasing productivity.
According to a report published by Shelter, 250,000 new homes a year need to be built in the UK to keep up with demand – and yet only 163,000 new homes were delivered in 2017. The unprecedented demand for new housing has created a systemic crisis.
There is a severe shortage of affordable homes and homelessness continues to increase year on year. There is a lack of skilled labour in construction, compounded by Brexit, and an ageing workforce. The building industry has a poor delivery record with too many projects still fraught with sub-standard quality, delays and budget overruns. To quote one recent article – ‘too few homes, built at too high a price, for too few people’.
In response, the Government has set a target to build 300,000 new homes annually by the mid-2020s and has pledged its support to increase the use of offsite construction to help address the challenges. This commitment is reinforced by the House of Lords committee report into offsite manufacture which called for a radical overhaul of the construction industry.
Surge in interest in modern construction methods
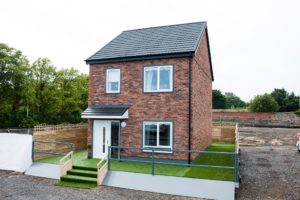
McAvoy prototype house
There has been a surge in interest in new construction methods in recent years, and particularly in offsite solutions, as traditional ways of working continue to fall short of the required standards and volumes. The UK construction industry has often been slow to adopt new technologies and processes – which is why it now has one of the lowest productivity rates in Europe.
Offsite construction though is not new – modular building systems have been widely used for decades from schools and healthcare schemes to hotels, commercial buildings and infrastructure projects. But are the skills transferrable? Our view is there is far less risk in using an offsite manufacturer with a proven track record, readily available production capacity, and who already has expertise as a principal contractor.
How to simplify procurement and improve quality control
There are now multiple options in the UK offsite housing sector for manufacturers to produce structures which are installed onto pre-prepared foundations – leaving design, groundworks and other aspects of the project to others.
In our experience, this approach is far less efficient and quality control issues can arise where there is no single point of contact. Another option is to give developers and housing providers a fully seamless turnkey service encompassing design, planning approvals, site preparation and groundworks, building manufacture, offsite fitting out, landscaping and infrastructure. This type of solution delivers improved quality control, effective cost management, and simplifies procurement and project management for the client.
Understanding the benefits
There are clear benefits of building new homes in a factory, which have been well documented and are demonstrated with the use of offsite solutions in other sectors.
Build programmes can be halved for a faster return on investment and earlier handover for occupation.
The quality of factory construction can far exceed site-based building methods. Offsite is not affected by poor weather or damage to materials on site. It is not reliant on subcontracted labour but instead uses a highly trained, permanent and multi-skilled workforce, manufacturing buildings in safe, purpose-designed factory environments. This has a hugely positive impact on the quality of construction. There is less disruption to neighbouring properties, fewer vehicle movements to sites, and far less material wastage.
With independent accreditations such as BOPAS – the Buildoffsite Property Assurance Scheme – developers, investors and lenders can now have the benefit of stringent assessments to certify that an offsite housing system will deliver consistent performance for at least 60 years. This significantly reduces risk and ensures long-term mortgageability.
The synergy between offsite housing and digital technology
There is tremendous synergy between offsite construction and the latest digital techniques, which give us the opportunity to radically improve the way we design and produce new buildings.
Harnessing the latest technology allows processes at the earliest stages of a project to be streamlined. Shorter design periods are critical for offsite construction. Manufacturing needs to start as soon as the ground is broken on site. To achieve that, detailed design information has to be released to manufacturing at a much earlier stage than with site-based construction – and that necessitates earlier decision making on the part of the client.
Digital construction allows a building design to be co-ordinated in a more efficient way and facilitates better quality decisions earlier in a project. If we use data rich, fully detailed 3D BIM models and walkthroughs, we can communicate a building design much more effectively, and present design options for discussion with stakeholders and planning authorities that are easier to view, simpler to follow and revise at the earliest stage.
Case Study – Helping to meet the shortfall in affordable housing
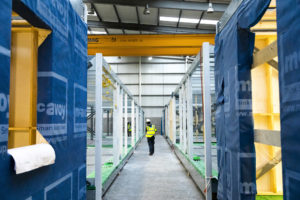
McAvoy Group Dungannon and Lisburn factories
The McAvoy Group is manufacturing the first offsite housing scheme to be built in Northern Ireland – a £4.7M contract for Clanmil Housing Association.
Now on site, the Joymount development will provide 40 much needed homes to help address the severe shortfall in social and affordable housing. There are currently 24,000 households in housing stress in Northern Ireland alone.
Due for completion in spring 2019, the scheme will feature apartments for couples and active older people, and two-bedroom family houses. There will also be three detached bungalows specifically designed for individual families with complex needs.
The McAvoy offsite solution will reduce the build programme by around 60 per cent on this scheme.
According to Carol McTaggart, Group Director of Development at Clanmil, “We want to be able to deliver new homes more quickly for people on the housing waiting list whilst still maintaining our high standards of design and build quality. We also need a solution that will deliver a range of energy-efficient homes with affordable running costs for our tenants.”
“By using advanced offsite construction technology, we believe we can shorten the programme for these 40 new homes by around 56 weeks which is crucial to reducing waiting lists.”
What the offsite industry needs now are more enlightened clients, such as Clanmil Housing Association, with the passion and commitment to break the mould and apply new techniques to deliver growth. To help address the challenges around productivity, reliable delivery, quality and the affordability of new housing, developers in both public and private sectors should be willing to adopt more innovative building techniques. We will then be able to revive the ailing housebuilding sector.
If you would like to read more articles like this then please click here.
The post How offsite is set to revive the ailing housebuilding industry appeared first on UK Construction Online.
Walang komento:
Mag-post ng isang Komento