Commentators from the construction industry may be wondering what the rest of 2018 will hold for the sector. Q1 was incredibly bumpy – the collapse of Carillion in the first few weeks of January, the Beast from the East and ongoing uncertainties with Brexit meant firms faced unprecedented challenges.
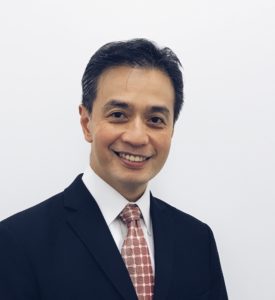
Stanley Chia
Stanley Chia, Senior Vice President for Tungsten Network discusses the situation.
While the latest IHS Markit/CIPS construction figures for April show an uplift, this is perhaps inevitable after the industry’s poor start to the year. The Purchasing Managers Index rose to 52.5 in April, its highest level for five months, having sunk to a 20-month low of 47.0 in March. Anything above 50 indicates a moderate expansion of overall construction output.
Hopefully, housebuilding, commercial building and civil engineering activity will continue to fuel the recovery, but it’s clear there are systemic issues within the sector that hold it back.
Pre-digital methods
While the modern supply chain is entering a new era, too many construction businesses are still using archaic, paper-based invoicing rather than embracing newer, streamlined digital systems. This isn’t just a shame – it has huge consequences. Reliance on paper in the finance department, manually entered data, and countless other dated practices leave too much room for friction in the procure-to-pay process.
After the collapse of Carillion, it was revealed some suppliers were waiting as long as 120 days to receive payment from Carillion, many probably unaware of what stage invoices were at and feeling powerless to fight the late payment contagion. As a result, the government has vowed to implement an urgent crackdown on the late payments crisis, but legislation can only go so far. If construction companies run their back-office operations in an outdated and pre-digital way, productivity will continue to be hampered.
Since 1994, according to the Office for National Statistics, UK output per hour has improved by 60% in the manufacturing industry, 30% in services, but only five per cent in construction.
Why is this? In my opinion, too many construction companies are resisting digital transformation.
Embracing technology to boost business
Research conducted by Tungsten Network, in partnership with Forrester, supports this view. It found that the victors in the digital age will be the companies that best use technology to win, serve, and retain customers. It also found that too often supply chains and procurement practices are not yet optimised to meet the demands of today’s customers.
When asked, both buyers and sellers – regardless of industry – outlined their many shared challenges, including cyber fraud, siloed data, insufficient cash, and legacy technology. These challenges distract from higher priorities, such as customer experience, product and service quality, and – crucially for the construction industry – operational agility.
It’s important to note that construction is not the only industry falling behind. A recent Gartner survey found that only 42 per cent of CEOs have begun digital transformation, while 451 Research’s Voice of the Enterprise Digital Pulse study showed that 60 per cent of organisations have no formal transformation strategy in place.
Despite this, many are feeling the pressure to transform how they run their businesses. PwC’s latest CEO Survey revealed that speed of technological change and cyber threats are among the top ten things CEOs worry about.
So why is it so difficult to bring the digital revolution into an organisation? What is it about new technology that sparks such fear and how can construction bosses buck the trend?
Most probably, it is the fear of the unknown and sometimes simply knowing where to begin. So much attention is given to customer-facing systems and processes and how they can be modernised that areas such as accounts payable, invoicing and supplier monitoring can easily be left behind. All too often a construction firm might update its website without thinking about its back office, paper-based and manual systems. If the goal is an agile and productive business the work must start from within.
A revolution with financial benefits
By moving from a manual invoicing system to an electronic one, businesses stand to save tens of thousands of pounds each year as digitising the payment process reduces the cost of handling invoices by more than 50%. The shift is a major one, however, and one that has to be handled with care.
When companies digitise their payment processes, everyone benefits. Electronic invoicing increases the efficiency, accuracy and productivity of the accounts payable team and it provides real-time data to optimise spending and support the procurement process. It also improves internal controls, reducing the potential for fraud and mistakes. For suppliers, they can have full visibility of their invoice status online, from confirmation of receipt to final payment meaning they no longer have to chase for payment. This strengthens supply chain relationships and helps tackle the late payment epidemic.
The truth is, many businesses are struggling with inadequate processes and it is impacting the bottom line. For businesses to thrive, they need to be properly managed using modern tools and processes that establish accountability, reduce uncertainty, and foster trust through creating a responsible supply chain. If the construction industry is to tackle its very real challenges – productivity and late payment to name just two – it’s time to stop sticking its head in the sand. Instead, firms need to look ahead and focus on removing friction from the construction supply chain by embracing what digital transformation can offer.
If you would like to read more articles like this then please click here.
The post When will the construction industry embrace digital transformation? appeared first on UK Construction Online.
Walang komento:
Mag-post ng isang Komento